
Technicians need to ensure that belt guards are properly installed and that debris is not falling into the drive path.
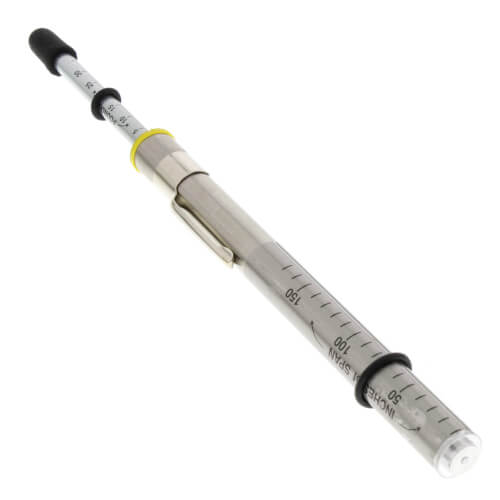
(See Figure 1.) A sheave gauge is an excellent tool for identifying sheave wear.Įnvironment is an often overlooked contributor to sheave wear. Note: Sheaves having greater than 1/32 inch wear need to be replaced. Technicians should check for proper alignment, installation, and tension. Technicians need to ensure that preventive maintenance programs/schedules incorporate inspection of driver and driven sheaves. Maintenance is a critical element to minimizing sheave wear. Even a slight wobble can cause premature sheave wear. Failure to properly install a bushing can cause wobble and vibration. Bushings must be properly installed so appropriate engagement with the sheave and shaft occurs. Technicians need to ensure that sheave alignment is achieved. Installation must be done correctly to avoid sheave wear. A tension checker is recommended for all installations and maintenance procedures to help ensure adequate tension. As a drive starts and stops, the constant slipping decreases belt life and erodes sheave grooves. If belts are undertensioned, they slip in the groove of the sheave.

Click on the image for an enlarged view.ĮXPLANATION Tension is often a leading cause of efficiency loss and leads to sheave wear.
